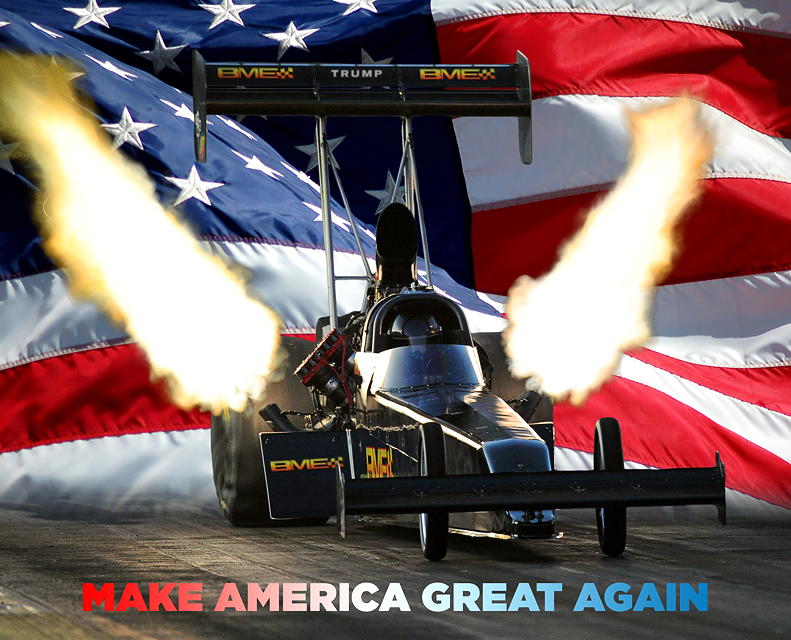
Image: AutoImagery
Racers Win with Bill Miller Engineering
Why do racers demand Bill Miller Engineering Forged Aluminum Connecting Rods, Forged Aluminum Racing Pistons, VascoMax Wrist Pins, and Supercharger Rotors?
Because BME products have excellent quality, unquestionable reliability, and are made with advanced manufacturing technology. That combination results in performance that wins races and clinches championships. Look at the results in just NHRA drag racing. BME engine components have won many championships at the highest level–the nitro classes. Most recently, in the 2024 NHRA Mission Foods Drag Racing Series, Antron Brown was Top Fuel Champion, and Austin Prock won the Funny Car title. Both used BME parts.
Since 1975, drag racers have become champions using Bill Miller Engineering Forged Aluminum Connecting Rods. John Force Racing, a team with 23 NHRA nitro class championships, campaigns a Top Fuel dragster and two Funny Cars. One reason JFR chose BME as a partner was its success with BME Aluminum Rods. The Rods have also taken import drag racing by storm, becoming a top choice of Honda, Nissan, and Toyota competitors. The World's quickest and fastest import, the SpeedFactory Honda Civic, shredded dragstrip clocks with a 6.65-second pass, and, in another run, went 217.77 mph. The SpeedFactory team uses BME Forged Aluminum Connecting Rods.
Bill Miller Engineering Forged Aluminum Racing Pistons have won nine Championships in NASCAR's three touring series, Camping World Truck, Xfinity, and NASCAR Cup. Australia hosts the most hotly-contested sedan road racing series in the World, the Repco Australian Supercars Championship. BME Pistons won that championship for seven years straight, 2009-2016. In 2025, Australian engine builders continue to put BME Forged Aluminum Pistons in their Supercar Series engines. In Drag Racing, BME Pistons have won championships in Top Fuel, Funny Car, Pro Stock, and Pro Mod. Bill Miller Engineering Pistons are widely used in import drag racing, including the SpeedFactory's mid-six-second, 2300-hp Honda.
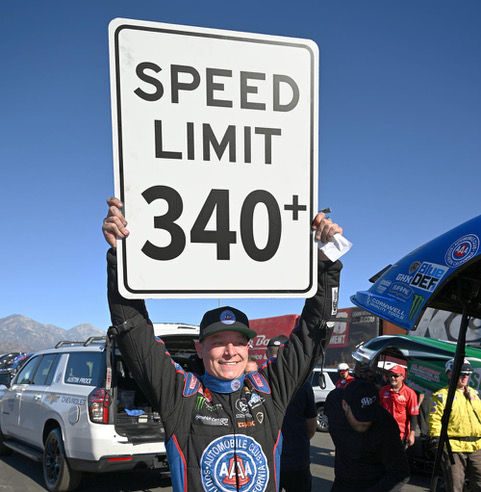
A jubilant Austin Prock after driving the BME-equipped "Prock Rocket" to a top speed of 341.68 mph at In-N-Out Burger Pomona Dragstrip on November 17, 2024. Image: NHRA
Bill Miller Engineering VascoMax Wrist Pins are another drag racing benchmark. They are the choice of John Force Racing. The team's Top Fuel Dragster and one of its Funny Cars hold NHRA speed records at 341.59 and 341.68 mph, respectively, making BME Wrist Pins the fastest in drag racing, but wait, there's more. In 2024 NHRA competition, 2/3rd of the Top Ten in points for both Top Fuel and Funny Car had BME Wrist Pins in their engines. The import racers, like the SpeedFactory Honda team, rely on BME Pins, too.
Bill Miller Engineering products are the fastest in land speed racing at the Bonneville Salt Flats. Two cars that hold records over 400 mph in the top classes for reciprocating internal combustion engines, AA/Blown Fuel Streamliner (AA/BFS), and AA/Fuel Streamliner (AA/FS), used BME parts. Our products have more time at 400+ MPH than those from any of our competitors.
At Bill Miller Engineering, all raw materials are American-sourced. Our Connecting Rods, Pistons, Wrist Pins, and Supercharger Rotors are 100% designed, developed, and manufactured in the USA. The BME mission is: 1) to manufacture the best-performing, highest-quality competition engine components and 2) to provide outstanding customer service. Give us a call or email us today to discuss how BME can make your racecar quicker, faster, as well as more consistent, reliable, and durable.